Understanding Injection Mold Plastics
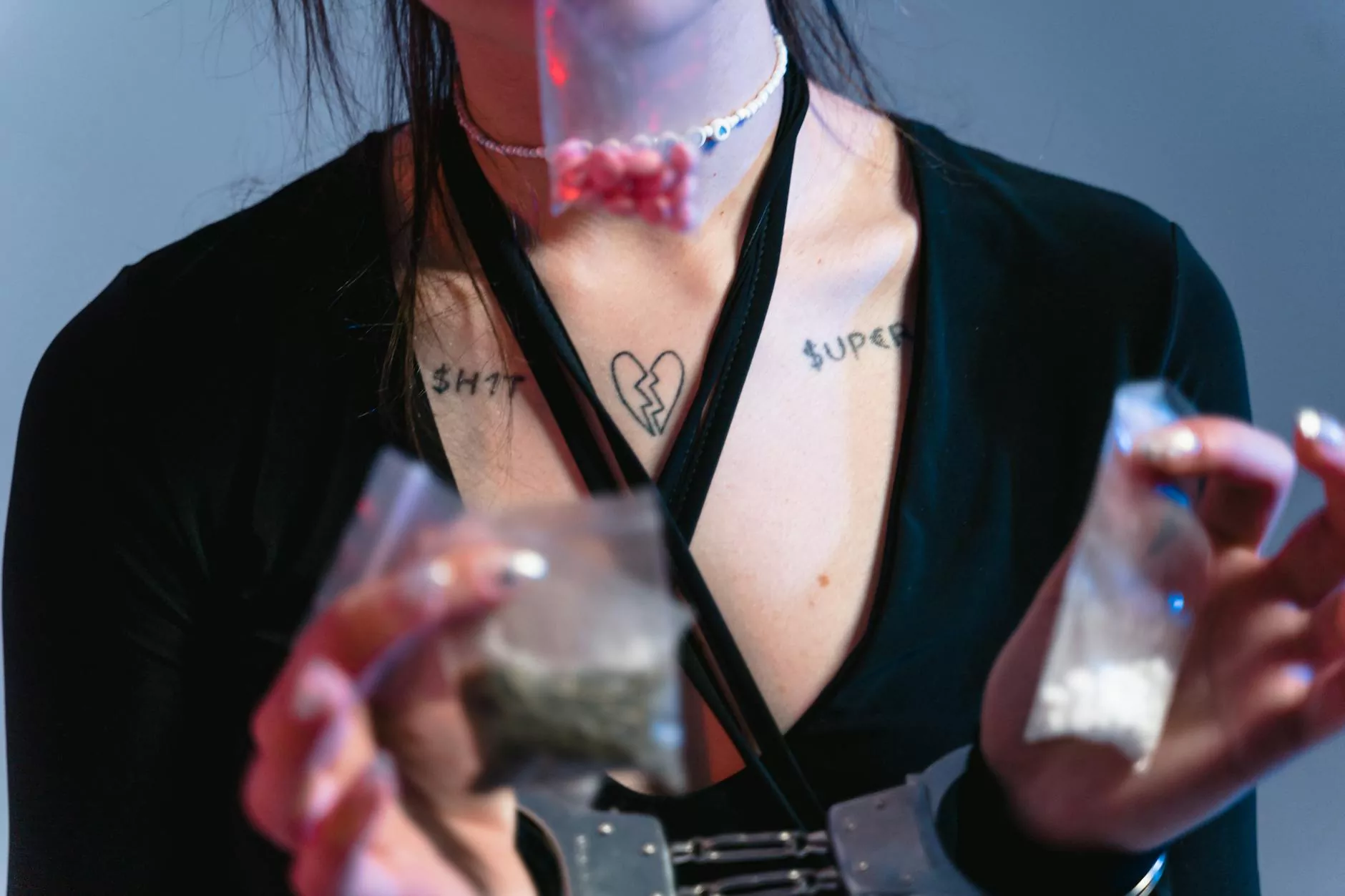
In today's competitive manufacturing landscape, injection mold plastics represent a cornerstone of innovation and efficiency. This article explores the ins and outs of injection molding, its benefits, applications, and how businesses can effectively utilize this technology to achieve remarkable results.
What is Injection Molding?
Injection molding is a manufacturing process where molten material is injected into a mold cavity. The material, which can be various types of plastic, hardens into the desired shape once cooled. This technique is particularly loved for its ability to produce complex shapes with high precision, making it essential for industries ranging from automotive to consumer goods.
The Science Behind Injection Mold Plastics
The primary materials used in injection molding are thermoplastics and thermosetting plastics. Thermoplastics can be reheated and reshaped, while thermosetting plastics are molded once and cannot be remolded. The choice between these involves understanding the application and desired features of the final product.
Types of Injection Mold Plastics
There are several types of plastics used in the injection molding process, including:
- Polyethylene (PE) - Known for its versatility and low production cost.
- Polypropylene (PP) - Offers a great balance of flexibility and rigidity.
- Polyvinyl Chloride (PVC) - Widely used for its chemical resistance and durability.
- Acrylic (PMMA) - Best known for its optical clarity and is often used as a glass substitute.
- Polystyrene (PS) - Commonly used for making disposable cutlery and containers.
Benefits of Using Injection Mold Plastics
Injection molding offers numerous advantages that can significantly enhance production processes:
1. Efficiency and Speed
The injection molding process allows for rapid production cycles. Once the mold is created, hundreds or even thousands of identical parts can be produced in a short period, making this method incredibly efficient for bulk manufacturing.
2. Cost-Effectiveness
While the initial investment in mold creation can be high, the per-unit cost decreases significantly with volume production. This makes injection molding cost-effective for large runs of components.
3. Design Flexibility
Injection mold plastics allow for complex designs that would be difficult or impossible to achieve with other manufacturing methods. Designers are only limited by their imagination when it comes to creating intricate details and sophisticated geometries.
4. Consistency and Precision
Injection molding is known for producing highly consistent parts with tight tolerances. This precision is essential for applications where uniformity is critical, such as automotive and medical devices.
5. Material Versatility
The ability to use various plastics means that manufacturers can select materials that best suit their application needs, whether they require durability, flexibility, environmental resistance, or aesthetic qualities.
Applications of Injection Mold Plastics
The range of applications for injection mold plastics is extensive. Here are some of the major industries that rely on this innovative technology:
1. Automotive Industry
Injection molding is heavily used in the automotive sector for producing parts like dashboards, panels, and various under-the-hood components. These parts require high durability while maintaining lightweight properties to enhance fuel efficiency.
2. Consumer Products
From household items to electronics, many consumer products are manufactured using injection molding. The capability for intricate designs allows for products that are not only functional but also aesthetically appealing.
3. Medical Devices
The medical industry benefits from the precision and reliability of injection molded components. Devices such as syringes, inhalers, and various surgical tools are manufactured this way to meet strict regulatory standards.
4. Packaging
Many packaging solutions, including bottles and containers, utilize injection molded plastics for their durability and customizability. This method allows for the economical production of large quantities of packaging while maintaining high quality.
The Injection Molding Process Explained
Understanding the steps involved in injection molding can help businesses better appreciate its capabilities. The process typically includes the following stages:
1. Mold Design and Fabrication
A mold is designed specifically for the part to be produced. This design phase is critical because it determines the part's final shape, features, and material flow. Once designed, molds are fabricated from steel or aluminum, depending on the production volume.
2. Material Preparation
The chosen plastic material is prepared, which may involve drying to remove moisture, as plastics are sensitive to moisture during processing.
3. Injection Phase
The plastic pellets are heated until they reach a molten state and then injected into the mold under high pressure. This pressure is essential for ensuring that the molten material fills every cavity of the mold.
4. Cooling
Once the mold is filled, the molten plastic is allowed to cool and solidify. The cooling time can vary based on the material and the geometry of the part.
5. Ejection
After cooling, the mold opens and the solidified part is ejected. This must be done carefully to avoid damaging the newly formed component.
6. Finishing
Post-processing steps might include trimming, painting, or additional assembly to meet the specifications of the final product.
Challenges in Injection Molding
While injection mold plastics have numerous advantages, there are also challenges to consider:
1. High Initial Costs
The cost of designing and fabricating molds can be substantial, which may pose a barrier for smaller businesses or startups.
2. Material Limitations
Not all plastics are suitable for injection molding. Businesses must carefully consider the material properties when selecting a plastic for their applications.
3. Complexity of Design
While injection molding allows for intricate designs, the complexity of the mold can lead to higher costs and longer lead times.
Conclusion
In conclusion, the realm of injection mold plastics is vast and filled with opportunities for businesses looking to innovate and enhance their product offerings. Companies like deepmould.net are at the forefront of this technology, providing expertise in the design and manufacturing of high-quality plastic components. By leveraging the benefits of injection molding, manufacturers can achieve efficiency, cost-effectiveness, and unparalleled design flexibility, ensuring their products meet the ever-evolving needs of the market.
Further Learning and Resources
If you're interested in diving deeper into injection molding and its applications, consider exploring the following resources:
- Cloud's Insights on Injection Molding
- DeepMould Injection Molding Services
- Plastics Industry Association
By understanding the fundamentals of injection mold plastics, you can make informed decisions that will benefit your business and lead you toward sustainable growth and success in a fast-paced market.