Industrial Vacuum System Design: Elevating Business Efficiency
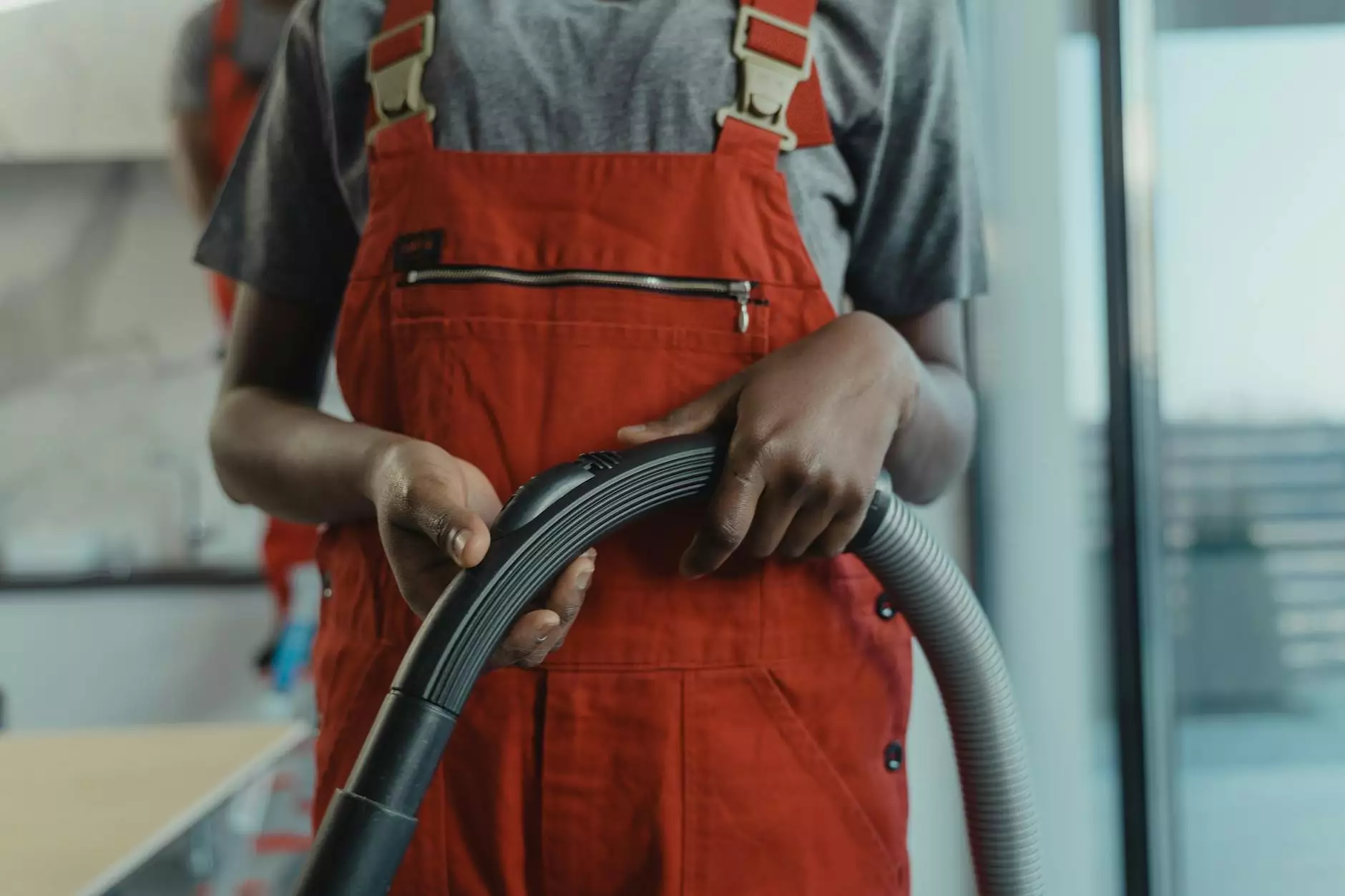
In today's competitive industrial landscape, adopting cutting-edge technologies and systems has become paramount. One integral aspect that many businesses overlook is the industrial vacuum system design. This article delves into the importance of these systems, the advantages they offer, and how a well-designed vacuum system can significantly improve operational efficiency in your business. We will explore various components, their functionalities, and best practices in vacuum system design.
Understanding Industrial Vacuum Systems
Industrial vacuum systems are sophisticated setups designed to remove unwanted materials from the air, surfaces, and processes within a facility. These systems are utilized in a variety of industries, including manufacturing, food processing, pharmaceuticals, and cleaning services. They play a crucial role in maintaining a clean environment, preventing contamination, and ensuring the safety of personnel.
Key Components of Industrial Vacuum Systems
To appreciate the complexity and importance of industrial vacuum system design, it's essential to understand its core components:
- Vacuum Pumps: The heart of any vacuum system, responsible for creating the vacuum pressure necessary to remove contaminants.
- Filtration Systems: Essential for trapping particles and ensuring clean air emissions, thereby protecting the environment and equipment.
- Hoses and Attachments: These determine the flexibility and reach of the vacuum system, allowing for tailored solutions in diverse settings.
- Collection Containers: Used to gather waste materials, which can be disposed of or recycled efficiently.
- Control Systems: To monitor and regulate the operation of the vacuum system, optimizing performance and minimizing energy consumption.
The Importance of Industrial Vacuum System Design
Effective industrial vacuum system design is not just about functionality; it’s about integrating aesthetics, usability, and efficiency. Here are several reasons why investing in a quality vacuum system design is crucial:
1. Enhanced Operational Efficiency
A well-designed industrial vacuum system increases productivity by minimizing downtime. Workers can maintain clean work areas, preventing interruptions in operations caused by contamination or equipment failure.
2. Improved Health and Safety
By effectively removing dust, debris, and hazardous materials from the workplace, industrial vacuum systems significantly reduce health risks. This ensures a safer environment for employees, thereby improving morale and productivity.
3. Compliance with Regulations
Many industries are subject to strict regulations regarding workplace cleanliness and air quality. A properly designed vacuum system helps businesses meet these necessary compliance standards, avoiding potential fines and enhancing their reputation.
4. Environmental Sustainability
A focus on industrial vacuum system design allows for more efficient waste management. Proper systems can facilitate recycling and waste sorting, leading to reduced landfill disposal and a smaller environmental footprint.
Factors to Consider in Industrial Vacuum System Design
When designing an industrial vacuum system, there are several factors that should be considered to tailor the system to the specific needs of your business:
1. The Type of Material Being Collected
The nature of the material, whether it be fine particulate, liquids, or large debris, will dictate the type of vacuum system required. Understanding the material properties is crucial for effective system design.
2. The Volume of Material
Knowing the expected volume of material to be collected helps in selecting the right size and capacity of the vacuum system. Overestimating or underestimating can lead to inefficiencies and higher operational costs.
3. The Layout of the Facility
Every facility is unique in its layout. A comprehensive understanding of the workspace layout allows for the optimal placement and length of hoses, ensuring the vacuum system covers all necessary areas without obstruction.
4. Energy Efficiency
In today's economy, energy costs can significantly impact operational budgets. Designing an energy-efficient vacuum system that operates effectively while consuming less power is paramount for sustainability and cost management.
Best Practices in Industrial Vacuum System Design
To maximize the effectiveness and longevity of your industrial vacuum system, adhere to these best practices:
1. Conduct a Comprehensive Needs Assessment
Before designing your system, conduct a thorough assessment of your company’s needs, including the types of materials, volumes, and working conditions. This will inform all subsequent design decisions.
2. Collaborate with Experts
Engage with professionals who have extensive experience in industrial vacuum system design. Their insights can guide you in making informed choices and avoiding common pitfalls.
3. Optimize System Layout
Plan the layout of the vacuum system for maximum efficiency. Ensure there are no kinks or sharp turns in hoses, which can hinder performance. A well-thought-out layout increases access to all areas of the work facility.
4. Prioritize Quality Components
Invest in high-quality pumps, filters, and hoses. The durability and reliability of these components will reduce maintenance costs and improve the overall efficiency of the vacuum system.
5. Regular Maintenance and Inspections
Construct a maintenance schedule to keep the vacuum system operating at peak efficiency. Regular inspections and cleanings prevent unexpected failures and ensure the longevity of the equipment.
Case Studies: Successful Implementation of Industrial Vacuum Systems
Examining real-world applications of industrial vacuum systems can provide valuable insights into their effectiveness:
Case Study 1: Manufacturing Industry
A leading automotive parts manufacturer implemented an industrial vacuum system to manage metal shavings and dust in their production area. This system not only enhanced workplace safety but also improved part quality, leading to significant cost savings and efficiency gains.
Case Study 2: Food Processing
A large food processing plant upgraded their sanitation process with a custom-designed vacuum system, which effectively removed waste and maintained compliance with health regulations. This resulted in improved product quality and reduced downtime caused by contamination.
Case Study 3: Pharmaceutical Facility
In a newly constructed pharmaceutical facility, the design team integrated a state-of-the-art vacuum system to handle Hazardous Pharmaceutical Waste. This system successfully created a safer working environment while ensuring adherence to stringent regulatory standards.
Conclusion: The Future of Industrial Vacuum System Design
As industries evolve and demand for cleaner, safer, and more efficient workplaces increases, the role of industrial vacuum system design becomes even more critical. By investing in high-quality systems, businesses not only ensure regulatory compliance and employee safety but also significantly enhance operational efficiency and environmental sustainability.
As you evaluate your own industrial processes, consider the profound impact that a well-designed vacuum system can make. Embrace innovation, invest strategically, and lead your business toward a future of success. For more information on tailored vacuum solutions, visit tmm.com.tr.