Exploring the Versatility of **Silicone Membrane** Technology
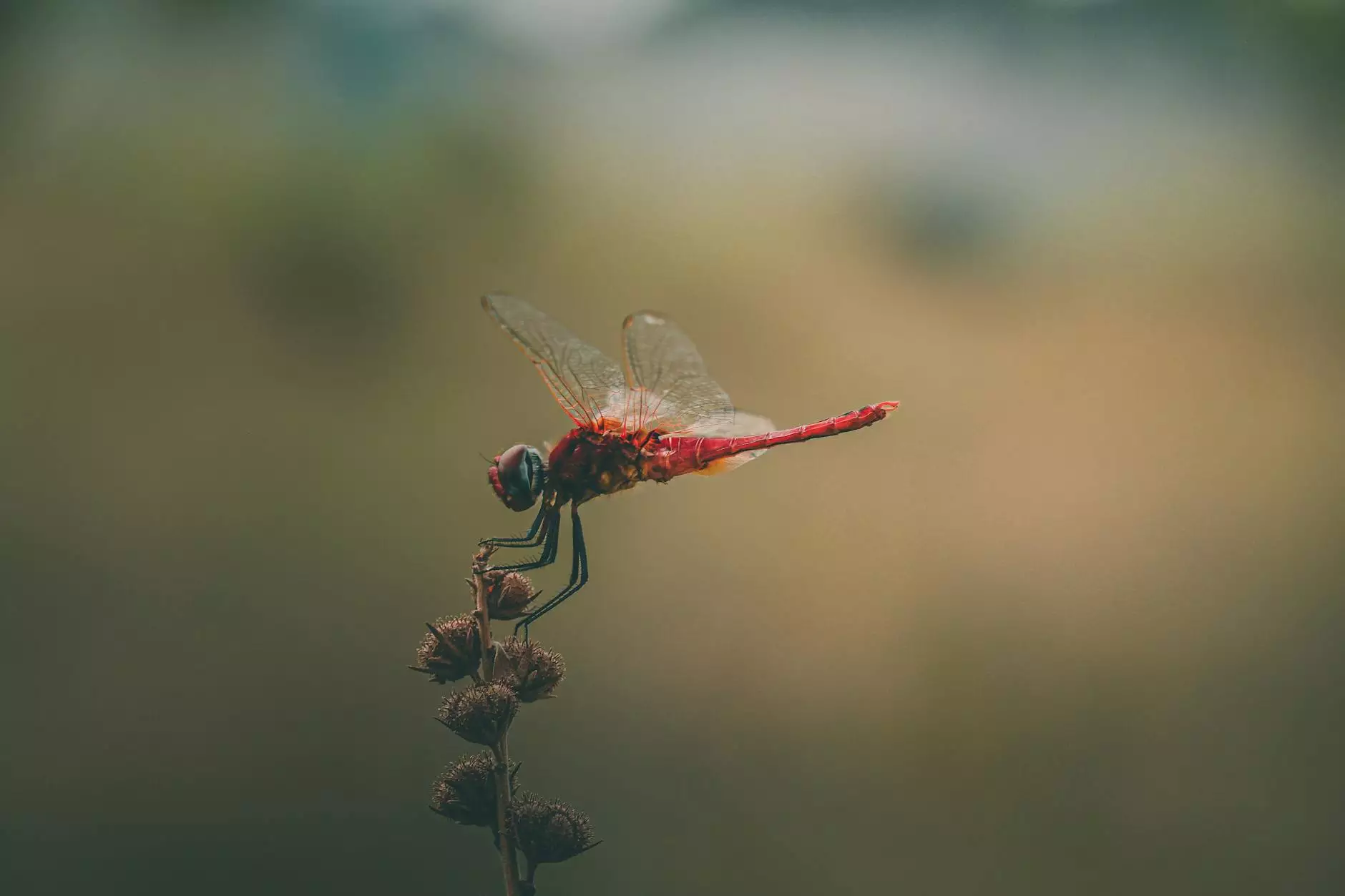
In the realm of industrial applications, silicone membranes have emerged as a crucial component in various processes. These membranes are renowned for their flexibility, durability, and effectiveness, making them indispensable in multiple sectors. In this comprehensive article, we delve into the functionality, advantages, and diverse applications of silicone membranes, offering insights that are vital for businesses looking to enhance their operational efficiency.
What is a Silicone Membrane?
A silicone membrane is a thin layer made from silicone rubber that exhibits outstanding elasticity and resistance to various environmental factors. These membranes are crafted through advanced technology that ensures high performance in numerous applications. Their unique properties allow them to be engineered for specific functions, making them ideal for everything from medical devices to automotive components.
The Advantages of Using Silicone Membranes
Silicone membranes offer numerous benefits that set them apart from other types of membranes, such as natural rubber membranes and various synthetic alternatives. Here are some of the most notable advantages:
- Durability: Silicone membranes are known for their exceptional longevity. They maintain their properties under extreme temperatures and exposure to various chemicals.
- Flexibility: The inherent elasticity of silicone allows these membranes to adapt to different shapes and sizes, making them versatile for a variety of applications.
- Temperature Resistance: Silicone can withstand high temperatures (up to 300°C) without degrading, which is critical for many industrial processes.
- Low Compression Set: Silicone membranes return to their original shape after compression, ensuring consistent performance over time.
- Biocompatibility: These membranes are often used in medical applications due to their non-toxic nature and compatibility with biological systems.
Applications of Silicone Membranes
The versatility of silicone membranes extends across numerous industries. Here are some of the primary applications where these membranes excel:
1. Medical Devices
In the healthcare field, silicone membranes are extensively utilized in devices such as catheters, surgical drapes, and sealants. Their ability to prevent contamination and maintain sterility is paramount in medical environments. Furthermore, their biocompatibility ensures patient safety, making them a go-to material for many manufacturers.
2. Automotive Components
In the automotive industry, silicone membranes serve crucial roles in systems requiring high durability and resistance to extreme temperatures, such as gaskets, seals, and vibration dampening components. These properties contribute to the longevity and reliability of vehicles, enhancing overall performance.
3. Industrial Applications
From vacuum systems to filtration technologies, silicone membranes are essential in industrial settings. Their ability to withstand harsh chemicals and extreme conditions enables their use in environments where other materials may fail. This includes applications in food processing, chemical manufacturing, and water treatment systems.
4. Electronics
Apart from mechanical uses, silicone membranes also play a crucial role in electronic devices. They can be found in sensors, keyboards, and touch panels due to their excellent electrical insulation properties and capacitive sensing capabilities, which greatly enhance product functionality.
Comparing Silicone Membranes with Other Membrane Types
When considering membrane options, it is essential to compare silicone membranes with alternatives such as rubber membranes and natural rubber membranes. Here’s how they stack up:
Silicone vs. Rubber Membranes
While both silicone and rubber membranes are used in various applications, silicone offers superior temperature and chemical resistance. Rubber membranes, although often less expensive, may not provide the same level of durability and elasticity, especially in extreme conditions. Consequently, businesses may opt for silicone membranes despite their higher initial cost, as the long-term performance and reliability often outweigh the upfront investment.
Silicone vs. Natural Rubber Membranes
Natural rubber membranes can deliver excellent performance in many applications; however, they are less resistant to heat and chemicals compared to silicone. This vulnerability can lead to faster degradation and reduced functional lifespan, particularly in high-stress environments. Therefore, for applications that require lasting durability and reliability, silicone membranes often prove to be the superior choice.
How to Select the Right Silicone Membrane for Your Needs
Selecting the appropriate silicone membrane involves several considerations to ensure it meets your specific requirements. Here’s a guide to help you navigate this important decision:
- Identify Your Application: Determine the environment in which the membrane will be used. Factors such as temperature extremes, chemical exposures, and mechanical stresses must be accounted for.
- Consider Membrane Thickness: Thicker membranes may be more durable but can also affect flexibility. Consider the balance between strength and flexibility based on your needs.
- Evaluate Elasticity and Compression Set: If your application requires frequent compression, choose a silicone membrane with a low compression set to ensure excellent performance over time.
- Check Manufacturer Certifications: Ascertain that the manufacturer adheres to industry certifications, particularly for medical or food-related applications where safety and quality standards are paramount.
- Seek Expert Consultation: Consider consulting with industry experts to tailor your selection based on detailed technical specifications and best practices in your field.
Investing in Silicone Membranes: Cost Considerations and ROI
While the initial cost of silicone membranes can be higher than traditional materials, the long-term benefits often justify the investment. Businesses can expect:
- Reduced Downtime: Durable silicone membranes minimize the risk of equipment failure, leading to decreased downtime and increased productivity.
- Lower Replacement Costs: The longevity of silicone membranes translates to fewer replacements, reducing material costs over time.
- Enhanced Product Quality: Using high-quality membranes can improve the overall quality of finished products, which may lead to increased customer satisfaction and loyalty.
Conclusion: The Future of Silicone Membranes in Business
The future of silicone membranes looks promising as technology advances. Innovations in production techniques and materials science will likely lead to even more efficient and effective silicone membranes, expanding their applications across industry boundaries.
Businesses focusing on adopting advanced membrane technologies can experience significant improvements in operational efficiency and product reliability. As you explore your options for buy membranes, consider the unique advantages that silicone membranes can offer over their counterparts.
For more details on acquiring silicone membranes, along with a comprehensive range of vacuum system parts and various other membrane types, visit us at vacuum-presses.com. Our experts are ready to assist you in making informed decisions to elevate your business.